Einführung
Die Nutzung von RICOHdie globale Fertigungs- und Innovationskompetenz von RICOH, Ricoh 3D seinen Kunden durch 3D-Druck und maßgeschneiderte End-to-End-Lösungen für die additive Fertigung (AM) die Möglichkeit, Mehrwert zu schaffen.
Ricoh 3D unterstützt die globale Vision von RICOH: Menschen zu befähigen, ihre Verwirklichung durch Arbeit indem wir verstehen und verändern, wie Menschen arbeiten, damit wir ihr Potenzial und ihre Kreativität freisetzen können, um eine nachhaltige Zukunft zu verwirklichen.
Und was wäre eine größere Erfüllung durch Arbeit als der erste übermenschliche Flug der Welt!
Geschichte
Von bescheidenen Anfängen zu einem Multi-Dollar-Unternehmen mit einer Vielzahl von Möglichkeiten in verschiedenen Sektoren… Einführung Schwerkraft Industrien.
Der Gründer, Richard Browning, arbeitete 16 Jahre lang in der Ölindustrie bei BP in London und war nebenbei sechs Jahre lang bei der Royal Marine Reserve. Aber im Nachhinein betrachtet stammt die Inspiration für den Jet Suit aus seiner Kindheit, als er bei seinem Vater, einem Luftfahrtingenieur, aufwuchs, in dessen Werkstatt bastelte und mit ihm Modellsegelflugzeuge flog.
Im Jahr 2016 begann Richards experimenteller Bauprozess. An seinen Abenden und Wochenenden kaufte Richard sein erstes Düsentriebwerk und durchlief dann endlose Prototyping-Versuche, bevor er im November 2016 den ersten Flug absolvierte.

In den nächsten sechs Monaten wurde das System weiter verfeinert, und es wurden Sponsoren gewonnen, so dass Gravity Industries im April 2017 offiziell an den Start gehen konnte. Das Unternehmen sicherte sich bald eine Investitionsfinanzierung in Höhe von 650.000 $ und so begann Richard mit einer Reihe von Fertigungsspezialisten zusammenzuarbeiten, darunter Ricoh 3D.
Und es war das Polypropylen von Ricoh 3D, das dazu beitrug, Richards Traum vom ‘übermenschlichen’ Flug Wirklichkeit werden zu lassen!
Klicken Sie hier, um die ganze Geschichte zu lesen.
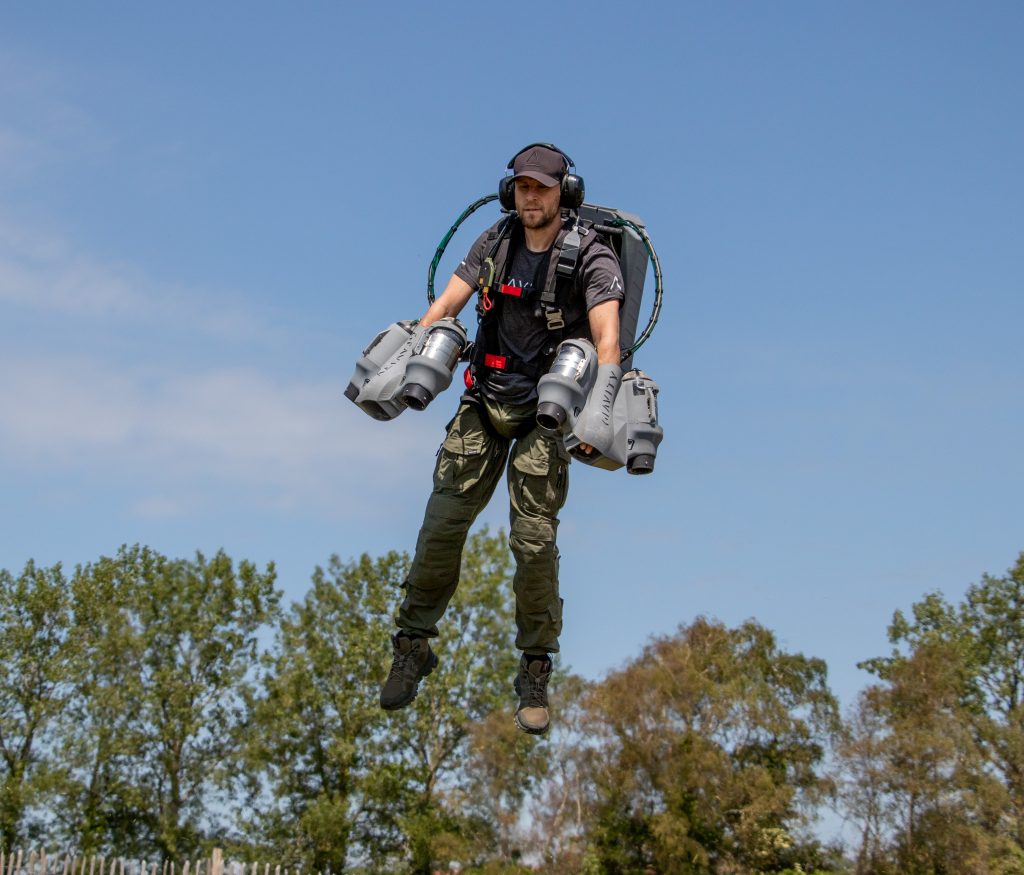
Die Entscheidung von Gravity, mit Ricoh 3D zusammenzuarbeiten, ergab sich aus dem Wunsch, Jet-Anzüge zu bauen, die Geist, Körper und Maschine verschmelzen. Dies erforderte letztlich ein Material, das organische Materie nachahmt und ein komfortables und sicheres Flugerlebnis ermöglicht. Das Vorzeigematerial von Ricoh 3D, Polypropylenerfüllte alle Kriterien.
Der Rest ist Geschichte… Spulen Sie bis heute vor – ein engagiertes Team von über 30 verschiedenen und talentierten Personen auf allen Kontinenten, über 105 Live-Flugveranstaltungen in 31 Ländern, ein Such- und Rettungspilotprojekt mit der Great North Air Ambulance (GNAA), eine internationale Rennserie und mehr. Wer sagt, dass Menschen nicht fliegen können?








Anwendung
Mit zahlreichen maßgeschneiderten Anwendungsteilen, Iterationen, anpassbaren Jet Suits (die Liste lässt sich fortsetzen!) hat Gravity in der jüngsten Partnerschaft erneut die Expertise von Ricoh 3D in Anspruch genommen, um ihr bestehendes Jetpack-Design zu verbessern und die Nachhaltigkeit zu erhöhen, indem das Gewicht reduziert wird – ohne Kompromisse bei der Festigkeit einzugehen. Kurz gesagt: Gravity wollte unnötiges Material einsparen, um Leistung und Effizienz zu verbessern.

Nach einer gründlichen “Discover”-Phase – ein Teil des “Discover Transform Sustain”-Ansatzes von Ricoh 3D – waren Gravity Industries und Richard Browning von der Verwendung von Isogrid-Oberflächengittern fasziniert. Diese Lösung wird von einer Optimierungssoftware unterstützt und ist für die Herstellung von hochsteifen und leichten Komponenten bekannt, die häufig in der Luft- und Raumfahrt eingesetzt werden.
Wieder einmal, getreu ihrem Motto, haben sie es gewagt zu fragen: “Was wäre wenn?”
Lösung
Mit einem kundenorientierten Ansatz leitete Charlie Kelsey, Junior Engineer bei Ricoh 3D, die Optimierungsphase unter Verwendung von nTop Software – der leistungsstärksten Software für die additive Fertigung, die von Fachleuten für einige der innovativsten Produkte der Welt eingesetzt wird.
Konkret nutzte Charlie die Möglichkeiten der Software, um aus den internen “Flächen” des Jetpacks dreieckige Waben auf Zellkarten zu erstellen. Diese Waben wiesen unterschiedlich dicke Balken auf, die in der Nähe der Scheitelpunkte des Anzugs für maximale Stabilität sorgten.



Über den Optimierungsprozess sagte Charlie: “Durch die Anwendung des dreieckigen Wabenkonzepts wurde nicht nur eine hohe Gewichtsreduzierung erreicht, sondern auch die strukturelle Integrität des Jetpacks beibehalten, was maximale Sicherheit für den Bediener gewährleistet.
“Die Funktionen und Möglichkeiten von nTop haben mit ihren impliziten Modellierungswerkzeugen erheblich dazu beigetragen, dies zu erreichen. Ich freue mich sehr darauf, in zukünftigen Projekten mit Gravity – und auch mit unseren anderen Partnern und Kunden – weitere Optimierungen wie diese durchzuführen.”
Ergebnisse
Kurz gesagt, dieses innovative Design führte zu einer Gewichtseinsparung von über 15 %, was die Leistung und Effizienz des Jetpacks erheblich verbesserte und es somit nachhaltiger machte.

Zeugnis
In einem früheren Interview sagte der Gründer von Gravity, Richard Browning: “Unsere Partnerschaft mit Ricoh 3D hat gezeigt, dass alles möglich ist, wenn man Unternehmertum und technologische Innovation miteinander verbindet.
“Wir haben seit 2017 eine erstaunliche globale Präsenz aufgebaut, und RICOH hat es uns ermöglicht, eine ‘unmögliche’ Idee in etwas Produktionsfähiges zu verwandeln.”

Mark Dickin, Head of Additive Manufacturing bei Ricoh 3D, fügte hinzu: “Alle Jet-Anzüge, einschließlich dieses neuesten Modells, sind ein Beweis für die Zähigkeit der Technik und, wie Richard sagt, ‘eine Mischung aus Geist, Körper und Maschine’.”
“Indem wir zunächst die Grenzen des 3D-Drucks und des Polypropylens ausreizten, haben wir nicht nur unser Know-how und unseren Einfallsreichtum unter Beweis gestellt, sondern vor allem auch die Nachhaltigkeit! Polypropylen ist zu 90 % recycelbar, leicht und flexibel und dennoch unglaublich haltbar – ideal für den Einsatz in der Luft.
“Wir freuen uns, dass wir Gravity bei diesem jüngsten Projekt dabei unterstützen können, ihre Jetpacks durch Designoptimierung noch leichter zu machen. Optimierung des Designs.
“In dieser speziellen Anwendung war der innovative Einsatz von Isogittern entscheidend für das Erreichen unserer gemeinsamen Designziele. Außerdem hat die Gewichtsreduzierung die Leistung des Jetpacks erheblich verbessert.
“Richard und sein Team überschreiten die Grenzen dessen, was wir dem Menschen zutrauen. Wir freuen uns, dass wir daran mitwirken konnten und unsere Partnerschaft fortsetzen können, um mehr nachhaltige Komponenten und Anwendungen zu unterstützen.