Overview
Oliver Moore, a Manufacturing Operator at Ricoh UK Products Ltd. (RPL), raised an innovative solution to improve workplace efficiency and safety on the CF18 – Inspection Station. Having worked at RPL for 2.5 years, and previously as a temporary employee for 4 years, Oliver identified a challenge in the process and took the initiative to address it. His idea led to the design and production of bespoke pucks for supporting Toner Bottles during quality checks, helping to minimise toner spillage. This contribution aligns with Ricoh UK Products Ltd.’s Continuous Improvement culture, which encourages employees to take an active role in optimising processes and enhancing safety across operations. Oliver’s proactive approach not only improved workflow but also demonstrated the company’s commitment to fostering a mindset of ongoing innovation and refinement.
Problem
At the CF18 – Inspection Station, senior operators perform quality checks on toner bottles. Oliver noticed that there was no dedicated space to place the toner bottles, leading to operators precariously balancing the bottles, which often resulted in toner spills. This inefficiency posed a risk of material waste and disrupted workflow.
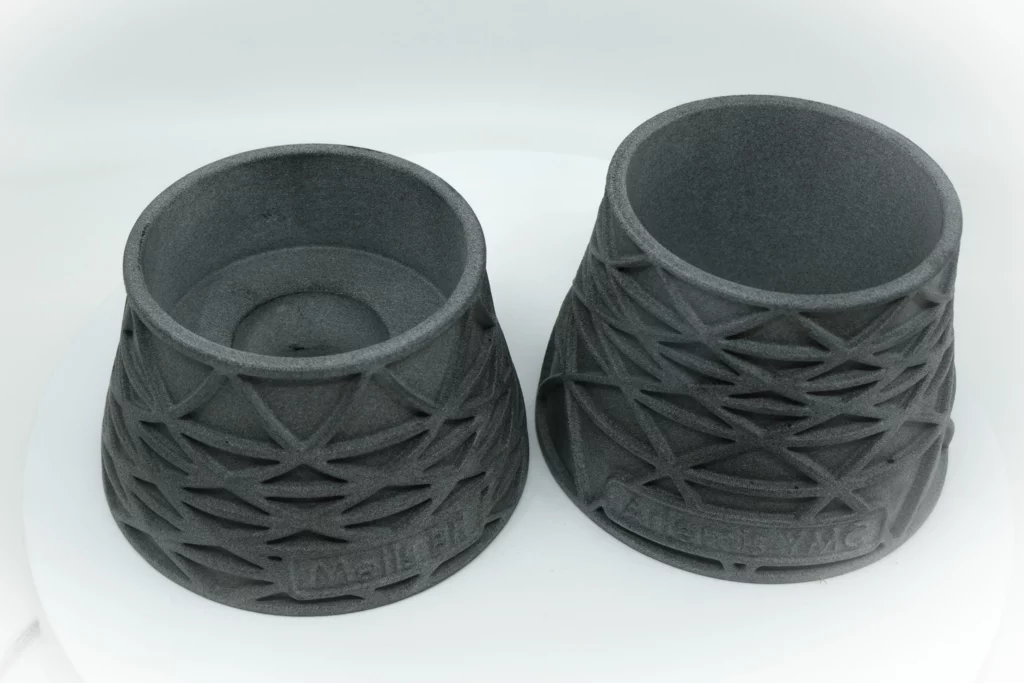
Solution
The solution was to create a custom-designed puck that would serve as stable supports for the toner bottles during checks. Recognising that RPL had the resources to create these in-house, Charlie Kelsey from the Ricoh 3D team, was approached to collaborate on the project.
The process began with Oliver presenting six different bottle types that required bespoke pucks.
Charlie from the 3D team worked closely with Oliver to:
– Visit the Gemba to understand how the pucks would be used in real operations.
– Design custom parts for each of the six bottle types.
– Use nTop software to integrate surface lattice designs into the pucks for cosmetic and lightweighting purposes.
– 3D print the parts using MJF PA12, a durable material ideal for this application.
The pucks were first implemented onto one of Ricoh UK Products filling lines for validation and testing. Following the successful trial, they were further deployed across all ten filling lines in two areas, with potential for further rollout across other Ricoh factories.
Additional Developments
As the pucks were used in daily operations, further improvements were made. Additional pads were added to the bottom of the pucks to enhance their grip, reducing the risk of slipping during use. These improvements helped extend the application of the pucks to other areas such as quality control (QC).
The 3D-printed pucks were customised with labels to match specific bottle types, ensuring standardisation across the process.
Impact
This initiative aligns with several of Ricoh’s Key Fundamentals:
Think Safety; Act Safely – The pucks contribute to a safer work environment by reducing toner spills and minimising the risk of accidents.
Embrace 5S – By introducing an organised solution for bottle placement, the pucks support a clean and efficient workplace, eliminating clutter and maintaining order.
Deploy Standardisation – The pucks help standardise the process across different areas, ensuring consistent and efficient operations.
Recognition and Acknowledgement
Oliver’s contribution was highly valued by his colleagues. Jon Frost, shift supervisor at RPL, praised his commitment and initiative:
“Oli is a Toner Operator, often tied to processes, but he goes the extra mile to make time and has always been keen to share his improvement ideas. His ideas have been recognised and celebrated in our team. He showed true passion for innovation, ensuring his idea was implemented from start to finish through communication with the AM department. This is a great example of why we encourage the teams to lead from the frontline, seek out solutions and improve our processes. Oli has exceeded our expectations, demonstrating personal growth, and his efforts should be recognised across the department and beyond.”
Oliver himself expressed his satisfaction with the project:
“My first port of call was to go to our internal Ricoh 3D team rather than an external supplier. I thought it would naturally be more cost-effective and foster collaboration within RPL. A big thank you to Charlie for your support.”
Bright Ideas Scheme
Oliver submitted this project through RPL’s Bright Ideas Scheme, a programme that encourages employees to suggest improvements and innovations. Launched in 2006, the scheme allows employees to contribute to the company’s continuous improvement efforts across areas such as safety, quality, cost, and delivery.
The scheme also recognises suggestions on a monthly and annual basis, awarding certificates and monetary rewards to employees who contribute to the business’s success. Oliver’s suggestion was an excellent example of the scheme in action, showing how employee-driven innovation can bring tangible benefits to the workplace.
Conclusion
The Puck solution is a testament to how employee-driven innovation can drive operational improvements, foster workplace safety, and enhance standardisation. By taking the initiative and collaborating with the Ricoh 3D team, the solution helped improve efficiency at RPL and is now being adopted across multiple areas of the business.