Introducción
Aprovechando RICOHde fabricación global e innovación, Ricoh 3D capacita a sus clientes a través de la impresión 3D y soluciones integrales de fabricación aditiva (AM) a medida, para crear valor añadido.
Ricoh 3D apoya la misión-visión global de RICOH: capacitar a las personas para que encuentren la plenitud a través del trabajo comprendiendo y transformando la forma de trabajar de las personas para que podamos liberar su potencial y creatividad y hacer realidad un futuro sostenible.
¡Y qué mayor Realización a través del Trabajo que lograr el primer vuelo sobrehumano del mundo!
Historia
De humildes comienzos a una organización multimillonaria con multitud de oportunidades en todos los sectores… Presentación Industrias Gravity.
El fundador, Richard Browning, pasó 16 años en la industria petrolera trabajando para BP en Londres y, paralelamente, pasó seis años en la Reserva Real de la Marina. Pero en realidad, en retrospectiva, su inspiración para el Jet Suit surgió de su infancia, cuando crecía junto a su padre ingeniero aeronáutico, jugueteando en su taller y volando con él en aeromodelismo.
En 2016, comenzó el proceso de construcción experimental de Richard. En sus noches y fines de semana, Richard compró su primer motor a reacción y luego avanzó a través de interminables intentos de creación de prototipos antes de lograr el primer vuelo en noviembre de 2016.

Durante los seis meses siguientes se perfeccionó el sistema y se consiguieron patrocinios, lo que permitió a Gravity Industries lanzarse oficialmente en abril de 2017. La empresa no tardó en conseguir una financiación de 650.000 dólares, por lo que Richard empezó a colaborar con varios especialistas en fabricación, entre ellos Ricoh 3D.
Y fue el polipropileno de Ricoh 3D el que ayudó a hacer realidad el sueño de Richard de un vuelo “sobrehumano”.
Haz clic aquí para leer la historia completa.
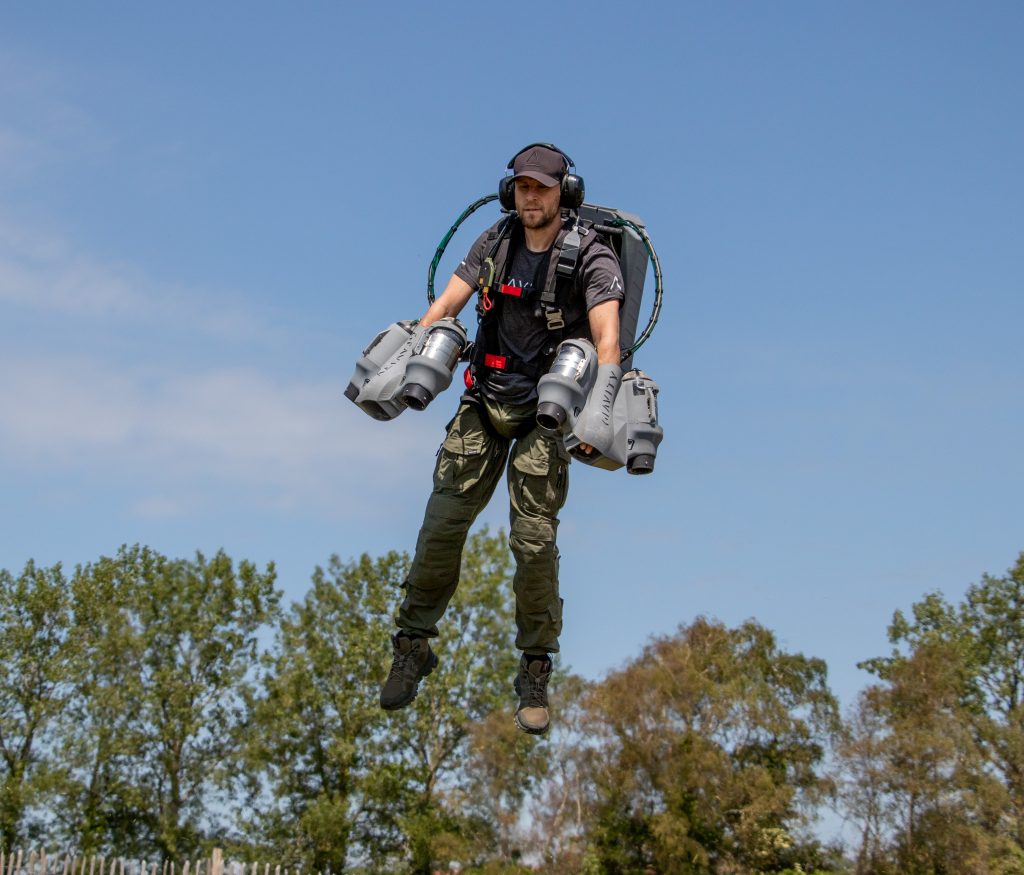
La decisión de Gravity de trabajar con Ricoh 3D surgió de su deseo de construir trajes a reacción que fusionaran mente, cuerpo y máquina, lo que en última instancia requería un material que imitara la materia orgánica y permitiera una experiencia de vuelo cómoda y segura. El material estrella de Ricoh 3D polipropilenocumplía todos los requisitos.
El resto es historia… Avanzamos rápidamente hasta hoy: un equipo dedicado de más de 30 personas diversas y con talento en todos los continentes, más de 105 eventos de vuelo en directo en 31 países, un proyecto piloto de Búsqueda y Rescate con la Great North Air Ambulance (GNAA), una Serie de Carreras Internacionales y mucho más. ¿Quién dijo que la gente no puede volar?








Aplicación
Con múltiples piezas de aplicación a medida, iteraciones, Jet Suits personalizables (¡la lista continúa!), en la última colaboración, Gravity buscó la experiencia de Ricoh 3D una vez más para mejorar su diseño de jetpack existente, y mejorar la sostenibilidad, reduciendo el peso, sin comprometer la resistencia. En resumen, Gravity pretendía eliminar material innecesario para mejorar el rendimiento y la eficacia.

Tras llevar a cabo una exhaustiva fase de “Descubrimiento”, que forma parte del enfoque empresarial “Discover Transform Sustain” de Ricoh 3D, Gravity Industries y Richard Browning quedaron intrigados por el uso del entramado de superficies isogrid, una solución impulsada por software de optimización, conocida por producir componentes de gran rigidez y ligereza, de uso habitual en aplicaciones aeroespaciales.
Una vez más, siguiendo su lema, se atrevieron a preguntar “¿y si…?”.
Solución
Con un enfoque centrado en el cliente, el ingeniero junior de Ricoh 3D, Charlie Kelsey, dirigió la fase de optimización, utilizando nTop el software de diseño de fabricación aditiva más potente, empleado por profesionales que hacen posible algunos de los productos más innovadores del mundo.
En concreto, Charlie aprovechó las capacidades del software para crear panales triangulares en mapas de celdas a partir de las “caras” internas del jetpack. Estos panales presentaban vigas de grosor variable, asegurando la máxima resistencia cerca de los vértices del traje.



Hablando del proceso de optimización, Charlie dijo: “Al adoptar el enfoque de panal triangular, no sólo se consiguió una gran reducción de peso, sino que también se mantuvo la integridad estructural del jetpack, lo que garantiza la máxima seguridad para el operador”.
“Las funciones y capacidades de nTop ayudaron significativamente a conseguirlo, utilizando sus herramientas de modelado implícito. Estoy deseando llevar a cabo más optimizaciones como ésta en futuros proyectos con Gravity, así como con nuestros otros socios y clientes.”
Resultados
En resumen, este diseño innovador permitió un ahorro total de peso de más del 15%, mejorando significativamente el rendimiento y la eficacia del jetpack, haciéndolo así más sostenible.

Testimonio
En una entrevista anterior, el fundador de Gravity, Richard Browning, declaró: “Nuestra asociación con Ricoh 3D ha demostrado que todo es posible cuando se combinan el espíritu empresarial y la innovación tecnológica.
“Hemos construido una huella global asombrosa desde 2017, y RICOH nos ha permitido transformar una idea ‘imposible’ en algo viable para la producción”.

Mark Dickin, Jefe de Fabricación Aditiva de Ricoh 3D, añadió: “Todos los trajes a reacción, incluido este último modelo, son un testimonio de la tenacidad de la ingeniería y, como dice Richard, “una mezcla de mente, cuerpo y máquina””.
“Al principio, al ampliar los límites tanto de la impresión 3D como del polipropileno, demostramos experiencia e ingenio, pero, lo que es más importante, ¡también sostenibilidad! El polipropileno es reciclable en un 90%, ligero y flexible, sin dejar de ser increíblemente duradero, ideal para surcar los cielos.
“Ahora, con este último proyecto, hemos tenido el placer de ayudar a Gravity a aligerar aún más sus mochilas propulsoras mediante optimización del diseño.
“En esta aplicación concreta, el uso innovador del entramado de isomallas ha sido fundamental para alcanzar nuestros objetivos de diseño compartidos. Además, la reducción de peso ha mejorado enormemente el rendimiento del jetpack.
“Richard y el equipo están ampliando los límites de lo que creemos que el ser humano es capaz de hacer, así que estamos encantados de haber participado en esto y esperamos seguir colaborando, ya que queremos apoyar componentes y aplicaciones más sostenibles.”