Succès dans l’amélioration du poids de l’équipement de production d’énergie micro-hydroélectrique et dans la réduction significative du temps nécessaire à la création de l’équipement.
Au début de l’année, le président-directeur général de Ricoh Company Limited (RCL), Akira Oyama, a annoncé que Ricoh avait mené une étude innovante et perspicace sur la production d’énergie micro-hydroélectrique dans les stations d’épuration.
Par ailleurs, M. Oyama a indiqué que des imprimantes 3D avaient été utilisées dans le cadre d’une recherche appliquée sur les égouts, menée par le ministère japonais de l’aménagement du territoire, des infrastructures, des transports et du tourisme (MLIT).
WEeeT-CAM, une start-up interne lancée dans le cadre de la nouvelle initiative de création d’entreprise de Ricoh “TRIBUS”, a participé à l’étude visant à examiner le développement de générateurs d’énergie hydroélectrique imprimés en 3D.
L’étude a permis de vérifier son utilisation dans une station d’épuration grâce à une collaboration industrie-université avec Seabell Incorporated et le laboratoire Masashi YAMABE – Masahiro SETO du département d’ingénierie mécanique de l’Institut de technologie de Kanazawa.
L’étude a permis de produire plusieurs kW d’électricité en utilisant des équipements dont les pales sont 25 % plus légères et les corps principaux 15 % plus légers que les dispositifs de production d’énergie hydroélectrique conventionnels en métal.
Ricoh 3D est fière d’annoncer qu’elle a soutenu la phase de démarrage du projet en 2020. L’équipe a été chargée de générer trois commandes de pièces imprimées en 3D en PA12 et en polypropylène, qui ont été utilisées par le département R&D de RCL dans le cadre d’activités de prototypage et de développement.
Grâce au soutien initial de RPL, Ricoh Company Limited a tiré parti de la technologie des imprimantes 3D pour créer un micro-générateur hydroélectrique intégrant des pales imprimées en 3D et fabriquées à partir de matériaux dérivés de la biomasse. Comparée à une turbine hydraulique fabriquée à partir de matériaux d’imprimante 3D couramment utilisés, la turbine était plus de deux fois plus résistante qu’une turbine en métal. Il a été constaté que la résistance était maintenue même après avoir été placée sous l’eau pendant une longue période et qu’elle pouvait être utilisée pour la production d’énergie hydroélectrique à grande échelle.
L’étude a également permis de réduire considérablement la période de production, qui est passée d’environ un mois à trois jours. La partie de la roue à aubes a été fabriquée en résine pour une meilleure durabilité sous l’eau.
À l’avenir, l’électricité produite par ces dispositifs devrait être utilisée comme alimentation de secours dans les centres de prévention des catastrophes, dans les stations d’épuration, dans les systèmes de batteries qui fournissent de l’énergie pour la mobilité, ainsi que dans les robots d’inspection automatique à chenilles.
Outre l’installation de générateurs micro-hydroélectriques dans des stations d’épuration au Japon, Ricoh continuera d’étudier la possibilité d’introduire cette technologie en Europe, aux États-Unis et dans les économies émergentes – avec le soutien de Ricoh 3D.
M. Oyama a fait le commentaire suivant : “Ricoh continuera à résoudre les problèmes sociaux par le biais de ses activités commerciales et à fournir une valeur utile à la société.”
Contexte
Le processus de traitement des eaux usées permet aux déchets, au sable et à la saleté de se déposer. Les eaux usées sont ensuite pompées dans un réservoir pour décomposer les impuretés à l’aide de micro-organismes. Pour que ces micro-organismes restent actifs, il faut que l’eau soit constamment alimentée en oxygène, ce qui consomme environ 75 kWh*, une quantité considérable d’énergie électrique équivalant à environ 110 milliards de yens de factures d’électricité par an. Il est donc urgent de réduire la consommation d’électricité pour économiser l’énergie et réduire les coûts.
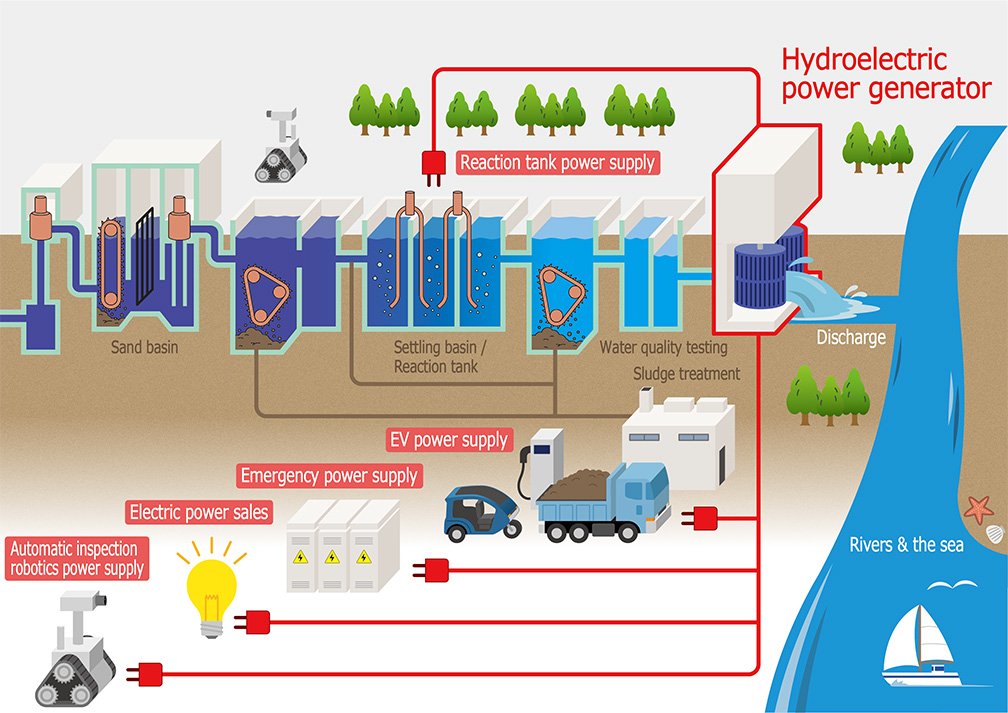
Certaines stations d’épuration utilisent actuellement des micro-générateurs d’énergie hydroélectrique, mais les équipements conventionnels posent les problèmes suivants : (1) faible efficacité de la turbine et faible rendement, (2) coûts d’achat et d’installation élevés des équipements de production d’énergie hydroélectrique, (3) l’importance de l’équipement pèse lourdement sur le personnel sur place, et (4) les équipements actuels de production d’énergie microhydroélectrique sont difficiles à utiliser dans des environnements qui exacerbent la rouille.
En réponse à ces problèmes, MLIT s’engage actuellement dans des démonstrations technologiques et des recherches appliquées pour réaliser des innovations vertes dans les systèmes d’assainissement. En mars 2022, une étude a débuté dans le domaine de la recherche appliquée aux systèmes d’assainissement, sur la base d’une proposition de Ricoh.
* Source : Subcommittee Report on Studies for Contributing to a Decarbonized Society, Sewage Policy Research Committee, publié par le MLIT japonais.
Détails de l’étude
La forme de la turbine hydraulique a été conçue en collaboration avec Seabell Incorporated, un fabricant spécialisé dans les micro-générateurs hydroélectriques à faible hauteur de chute, et l’Institut de technologie de Kanazawa. Des expériences de démonstration ont été menées dans une station d’épuration de la préfecture de Shizuoka, au Japon.
Le micro-générateur hydroélectrique utilisé comporte deux générateurs montés sur une seule unité, ce qui permet une production d’énergie efficace. En outre, comme il s’agit d’un dispositif de type ouvert, la roue à aubes peut être placée directement dans le cours d’eau existant, ce qui élimine la nécessité de construire un nouveau cours d’eau de dérivation pour la production d’énergie hydroélectrique et réduit le coût de la construction.
La technologie d’impression 3D de Ricoh a été utilisée pour créer un micro-générateur hydroélectrique intégrant des pales imprimées en 3D et fabriquées à partir de matériaux dérivés de la biomasse*. Comparée à une turbine hydraulique fabriquée à partir de matériaux d’imprimante 3D couramment utilisés, la turbine est plus de deux fois plus résistante** qu’une turbine en métal. Il a été constaté que la résistance était maintenue même après avoir été placée sous l’eau pendant une longue période et qu’elle pourrait être utilisée pour la production d’énergie hydroélectrique à grande échelle.
* Ressources organiques renouvelables dérivées d’organismes vivants ; ne comprend pas les ressources fossiles.
** Une contrainte maximale de rupture par flexion de 133 N/mm² en utilisant la méthode R3D New développée par Ricoh, comparée aux 60 N/mm² fournis par les caractéristiques de la résine des matériaux conventionnels.